The electronic lead screw is interesting. I've seen videos; Change gears would be no fun. Couple reasons I don't thread in reverse. One is I have a threaded spindle nose and there's always some (a small risk) risk of spinning the chuck off onto the ways. Second is I'm pretty good at hitting the groove where I end the thread, and trust me I try to thread at a pretty good clip. Experience. Third is the fact that most spindles are designed to take more thrust cutting toward the chuck.I converted to an electronic lead screw so it only runs when needed and I thread with the tool upside in reverse so there's no chance of a crash. I hated those sloppy change gears for threading. I also use WD-40 on aluminum. What year were your South Bend 9s made?
One of my little South Bends is 1947. 4 ft bed. I know because 1947 beds were different than the other two bed types used on them. They only made it that way 1 year. It's in very good condition. Hard to find them like that. But there are still a few out there. My other one 3 ft bed is from around the 60's or so because it has a plunger type tumbler gear selector. I think that started in the late 50's. And I also think SB9's were made up to '69.
I know I could get the exact date from Grizzly since they own South Bend for some time now but it doesn't matter to me. It's just trivia. The serial number on a SB is on the bed back near the lead screw bracket screws. An X in the serial # means special order. My later lathe has 2 X's. One is for the rare hardened bed. Very few SB9's have a hardened bed.
The reason we tend to lubricate aluminum when machining is it bonds to the cutting edge otherwise. I don't worry about it so much on a lathe because you can usually flick that off with your fingernail. For me it's more of an issue when drilling or milling. I'm not a fan of dumping oil all over everything I turn. It's just not necessary. A good finish is more so the result of proper tooling. Given that, a die maker told me to use kerosene on aluminum, even though it's not a secret as such, so I tried it and yes, it's the best! But I can get an excellent finish dry as well. Aluminum is easy, it's almost hard to not get a good finish.
I single pointed this little .166 x 36tpi thread right up to the shoulder last week. It's a proprietary thread tor a prewar BSA rifle. You can't let concerns about crashing distract you. If I do my eyeballs will start zig zagging as I near the stop. Be confident and focus.
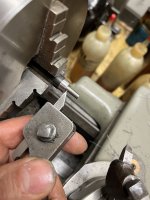
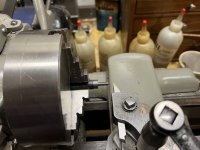
Upvote 0