OK, I've got a sherline mini lathe and I'd like to machine some o-ring grooves.
What type tool is best for cutting an o-ring groove in aluminum or delrin?
Are there specialized tools or cutters?
Could a thread-cutter be used?
ANd lastly, hat is the depth the groove should be cut..is it a percentage of the o-ring cross-section(thickness) measurement?
What type tool is best for cutting an o-ring groove in aluminum or delrin?
Are there specialized tools or cutters?
Could a thread-cutter be used?
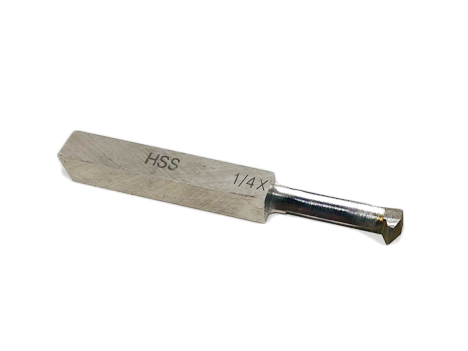
Right-Hand Internal Threading Tool - Sherline Products
www.sherline.com
ANd lastly, hat is the depth the groove should be cut..is it a percentage of the o-ring cross-section(thickness) measurement?